Atlas Bolt & Screw Co.
1. How do you determine which fastener is correct for your project? If it’s a pre-engineered metal building, the fasteners and their layout will be specified by the designer. If not, you’ll want to know what gauge metal you’re fastening to the building frame, and what the steel frame is composed of. If using self-drilling screws, you’ll want to ascertain that the drill point is long enough to drill through the panels and framing before the threads start to engage the metal. Be sure to have at least three full threads protrude from the back of the framing. Consider what diameter fasteners should be used. Will the fasteners require sealing washers? If using self-tapping fasteners, be sure to use the proper pre-drill bit size for the fastener and building frame thickness. Also consider options such as stainless steel- or zinc-headed fasteners for longevity and enhanced corrosion resistance.
2. Do you have any tips/tricks for metal to metal fastening?
Let the screwgun and the screw do the work. Start the drilling process slowly to let the point start to drill and then proceed to an appropriate RPM. If using longer length self-drilling screws, it is helpful to seat the screw against the panel, then turn the screwgun RPM up, stabilizing the screw and gun like a gyroscope. Then start the drilling process.
3. What are some common errors and how can they be avoided? Be certain that the nutsetter magnet is properly set for the screws you will be using. If the screws have sealing washers, take care to snug the washers against the panel but not crush them.
4. What kinds of tools do you advise for metal to metal fastening? The best tool for metal to metal fasteners is still a variable speed screw gun with a clutch and depth-sensitive nosepiece. Set the clutch to allow the operator to seat the screws securely. Be sure to use clean and good-fitting nutsetters. As always, have the appropriate PPE and have a safety review before starting the work.
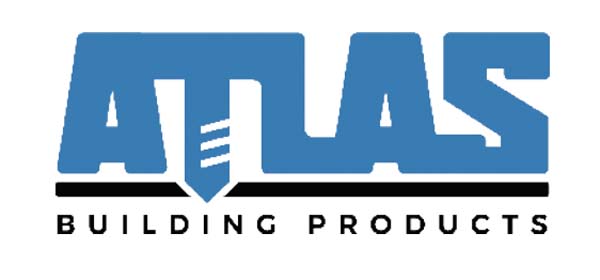
Direct Metals Inc.
1. How do you determine which fastener is correct for your project? The primary factor in a metal to metal self-drilling fastener application is the total thickness of the material one needs to penetrate. The drill point and flute combination need to be longer than the thickness of the metal. The higher the number of the point – 5 is maximum – the greater the steel thickness it will drill up to, 500” maximum. If it is too short, the point will stall during installation and will be unable to penetrate the metal. One must also consider insulation thickness between the metals. Most common is a fiberglass 2”-6” insulation that will compress to 1/8”-3/16”. In a pre-engineered steel building, there will be a #12 diameter structural fastener with EPDM sealing washer for the panel to roof purlin and a larger diameter ¼” “Stitch” or Lap fastener for a light-gauge panel to panel application. The larger diameter helps to prevent strip-out of the light gauge panels.
2. Do you have any tips/tricks for metal to metal fastening?
Metal roofing panels carry a 40 year or more warranty against red rust corrosion. Many building contractors continue to install metal to metal screws that do not carry a comparable warranty and only rely on zinc plating and additional coating to protect the fastener. It is strongly recommended to pair a fastener that carries a 40-year warranty with the metal panel, ensuring the warranty is intact. Choices include the DMI 304 SS Cap SCAMP self-drill or a zinc-aluminum alloy head. Both provide the protection needed and will not red rust. 304 stainless steel self-drilling screws exist, but are limited in availability and are very expensive.
3. What are some common errors and how can they be avoided? An exposed fastener roof panel is “compromised” with each fastener that is installed. It is critical for the installer to use a proper installation tool and technique. The fastener, the tool, and the installer are a 3-part component. Today’s light, battery- operated impact drivers are the tool of choice for metal to metal fasteners. However, these tools have no depth-sensing capability to ensure the fastener is driven to its proper depth without over-driving the sealing washer. A proper installation tool should have a torque setting or depth setting feature that allows for the fastener to be installed to a consistent depth every time. Battery drills and corded electric screw guns have this capability. A clean magnetic or spring loaded socket for non-magnetic fasteners will help prevent fracturing paint coatings on fastener heads.
If an installer takes a “craftsman” mentality and treats the fastener as an integral part of the roof system, he will greatly limit any potential future callbacks. Fasteners make up a very small percentage of overall building cost, but do account for a large majority of call backs because of improper installation.
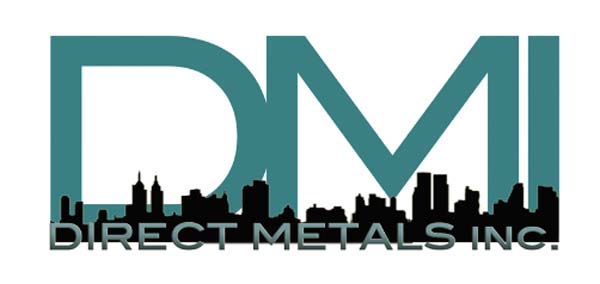
Dynamic Fastener
1. How do you determine which fastener is correct for your project? There are so many questions that must be considered before any purchase can be made. What is the material that I’m fastening? Am I working with dissimilar materials? Is the project in a highly corrosive environment where a long life-coated screw will need to be replaced by a stainless-steel screw? Will pullout and shear meet engineering requirements on the project?
2. Do you have any tips/tricks for metal to metal fastening?
When installing the T-1 and T-3 self-drilling screws, a 2,500 RPM screwgun should be used. A low 1,000 RPM/High Torque Tool is ideal for fastening T-5’s into ¼” and thicker steel. Self-Drilling screws for metal are designed to drill, tap and install in a one-step operation. With a drill tip on the end of each screw there is no need to pre-drill a hole as you would a tapping screw. The length of the drill bit on the fastener will determine the drilling capacity of the screw. T-1 point is used for sheet to sheet stitching with a total steel thickness of .024” to .095”. T-3, or a purlin screw, is used for a total steel thickness of .036” to .210”. T-4’s are used for a drilling capacity of .125” to .375”. T-5’s have a drilling capacity of .250” to .500”.
3. What are some common errors and how can they be avoided? Although not recommended, an impact driver will quickly install self-drilling screws, but the user must be cautioned to not over-torque the screw. An impact driver can easily shear off the head of the screw during installation. An over-torqued screw head could create excessive stress on the screw. This stress can fatigue the fastener over time, resulting in potential fastener failure after installation.
4. What kinds of tools do you advise for metal to metal fastening? Screw guns are available corded and also battery operated to handle just about any metal that needs to be fastened. It is critical that a Versa-Clutch torque adjustment system is used to allow you to “dial” the proper torque needed to efficiently drive fasteners without stripping or breaking the fastener.
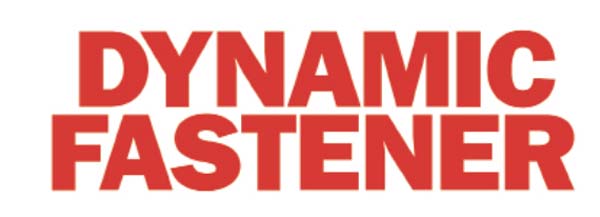
Beck America
1. How do you determine which fastener is correct for your project? It is dependent on the thickness of the material being fastened to the steel and the gauge of the steel. Beck offers solutions from 10 ga to 20ga.
2. Do you have any tips /tricks for metal to metal fastening? Good constant air pressure and volume are critical for ensuring pin installation is done properly. Use sequential fire versus bump and locate the pin near the web of the steel or the strong side of the stud to minimize deflection.
3. What are some common errors and how can they be avoided? Locating the fastener too close to the weak side or edge of the stud should be avoided. Using an air compressor that is too small for the job is another common error. Also, the material should be tight to the steel fastener.
4. What kinds of tools do you advise for metal to metal fastening? There isn’t a one-size-fits-all approach to this. It depends on the application or material and the thickness of the steel. There are a variety of tools to choose from including tools for trim, coil nailers, and RoofLoc™ for fast installation of metal roofing and facades.
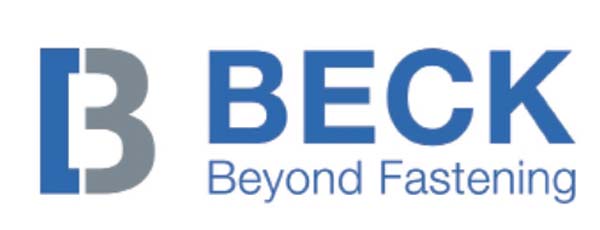
Levi’s Building Components
1. How do you determine which fastener is correct for your project? Substrate types are always the first step. (Metal to Wood/Metal to Metal/Etc)
Environmental conditions are also a key factor in determining the correct fastener for the job. Utilizing a long-life fastener can make or break certain critical exterior projects, as quality and performance come into play when fastening anything.
2. Do you have any tips/tricks for metal to metal fastening? An installer should be concerned about the speed of their drill. Allow the fastener to do the work. Impact drivers are not recommended because they use too many RPMs.
3. What are some of the common errors and how can they be avoided? Understand the thickness of the substrate that you are running the fastener into will determine the correct point. Knowing the thickness and choosing the right fastener will allow for more efficient labor time, and produce an overall better outcome.
4. What kinds of tools do you advise for metal to metal fastening?
Using a screw gun with a clutch that can run slow enough so that the tip can cut through the substrate is key. Using impact drivers and high-speed screw guns can cause failure of the fastener and cause delays or issues with job completion. RB
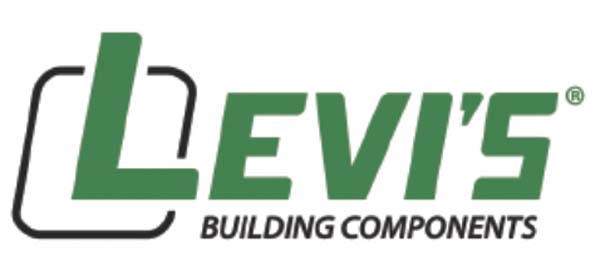