The resin is arguably the most important ingredient in the coating system because it determines the overall performance of the coating. As such, coatings are generally described by using the name of the type of resin used. There are three primary resin-based coating systems used for finishing metal building products: Polyester, Siliconized Modified Polyester, and 70% PVDF. The question is not necessarily which resin is the best, but rather, which coating formula is the right choice for the specific application. Each is discussed as follows.
Polyester
From good weathering, flexibility and hardness to corrosion resistance, this coating can be tailored with a combination of properties, making it an excellent multipurpose coating. Polyester coatings are a more economical option for general purpose applications and exterior surfaces that don’t see full sun. Typical uses include soffits and fascia, entry and garage doors, gutters, sheds and canopies.
Silicone Modified Polyester (SMP)
SMP offers a harder surface, better color retention and better weather resistance than polyester. Sherwin-Williams Coil Coatings uses the trade name WeatherXL™. This is probably our biggest product line in the ag business. It’s one of our biggest bread-and-butter items. We offer a smooth finish and, in recent years, added a product we call WeatherXL Crinkle Finish; it has a textured finish and has become a very popular product, especially for roofs. SMP coatings are commonly used in metal roofing and wall panels, pre-engineered building systems and agricultural building components.
Polyvinylidene Difluoride (PVDF)
PVDF is the most widely specified coating system for architectural projects—metal roof and wall panels. Sherwin-Williams Coil Coatings PVDF coatings, Fluropon®, represent a significant advancement in coating technology with superior weathering characteristics. They have long been recognized for their excellent chalk and fade resistance and are flexible in nature, allowing for the forming of a wide variety of shapes.
Adding to their appeal, PVDF coatings are available in a wide selection of colors. They are also commonly known as 70% PVDF coatings. It is important to understand that the percentage in 70% PVDF represents just the resin, and not 70% of the entire coating. The remaining 30% in the resin is comprised of acrylic.
PVDF coatings are especially effective in harsh environments where maintaining exterior appearance is just as important as long-term durability.
Coatings provide a barrier to prevent the metal from being exposed to oxygen, moisture, chlorides (salt) and chemical pollution.
High-build primers and clear coats can help ensure long-term performance against corrosion. High-build primers create a thicker barrier between the metal and pretreatments, which prevents moisture contact to the steel. Clear coats add another layer of protection on top of the coating against salts and chemical pollution, along with adding additional UV protection that can easily be cleaned.
Two-coat systems, standard primers and finish coats provide excellent performance in most environments. Specifically, thick film and chrome primers, along with a clear coat, are recommended in seacoast and industrial environments.
The Duranar XL Plus uses a thick film urethane primer, providing excellent adhesion and barrier protection, along with the Duranar color and clear coat, providing the best option for aggressive environments. Our PPG experts are able to work closely with our customers to determine customized coating systems that best fit their specific project, region and objectives.
TRINAR
TRINAR is a high-performance fluoropolymer coating containing a minimum of 70% polyvinylidene fluoride (PVDF) resin. This unique resin is combined with other proprietary resins, the highest quality ceramic and select inorganic pigments for the finest metal finish available. This two-coat system, using our High-Performance Primer, provides unparalleled protection against harsh environmental weathering. It has a tough but flexible finish, and meets or exceeds all requirements of AAMA 620/621 and AAMA 2605.
CERAM-A-STAR® 1050
CERAM-A-STAR 1050 is a silicone-modified polyester coil coating system designed exclusively for the metal construction industry. It has demonstrated superior durability and weather resistance through years of test data and installations in the field.
CERAM-A-STAR 1050’s proprietary resin formulation is combined with select ceramic and inorganic pigments, which are proven to be the most resistant to fade. In fact, the color stability of CERAM-A-STAR 1050 rivals that of 70% PVDF coatings, while offering excellent resistance to stains, scratches and abrasion. The result is a coating that provides the highest durability, consistency and color stability, making it ideal for residential, agricultural and commercial applications.
Cool Chemistry
Cool Chemistry products for roofing applications utilize ceramic and inorganic infrared reflective pigments. These special pigments are designed to reflect infrared energy while still absorbing visible light energy, thus appearing as the same color yet staying much cooler.
When cool chemistry coatings are used on metal roofing, the result is a sustainable building material that can lower air conditioning costs by up to 15%, reduce peak energy demand and help to mitigate urban heat island effects. Cool Chemistry pigments can be incorporated into any coating formula.
Coatings and metal substrates are applied to the roll formed panel before it is painted. These substrates are added to help protect the raw iron ore steel from corrosion.
For instance, Galvalume, a 55% Aluminum-Zinc alloy coating, behaves as a sacrificial element, sacrificing itself to help protect the steel. Oftentimes, in areas where moisture is prevalent, you will see a thin line of rust at the cut edge of a Galvalume panel. However, that rust is cosmetic and can generally be cleaned and will not worsen for some time. This is the Galvalume going to work to protect the steel. It acts as a buffer and “scabs over” to try and contain the corrosion of the steel.
In environments prone to high ammonia levels and corrosion, such as animal confinement, Galvanized, a zinc coating, has traditionally been a more highly sought-after solution.
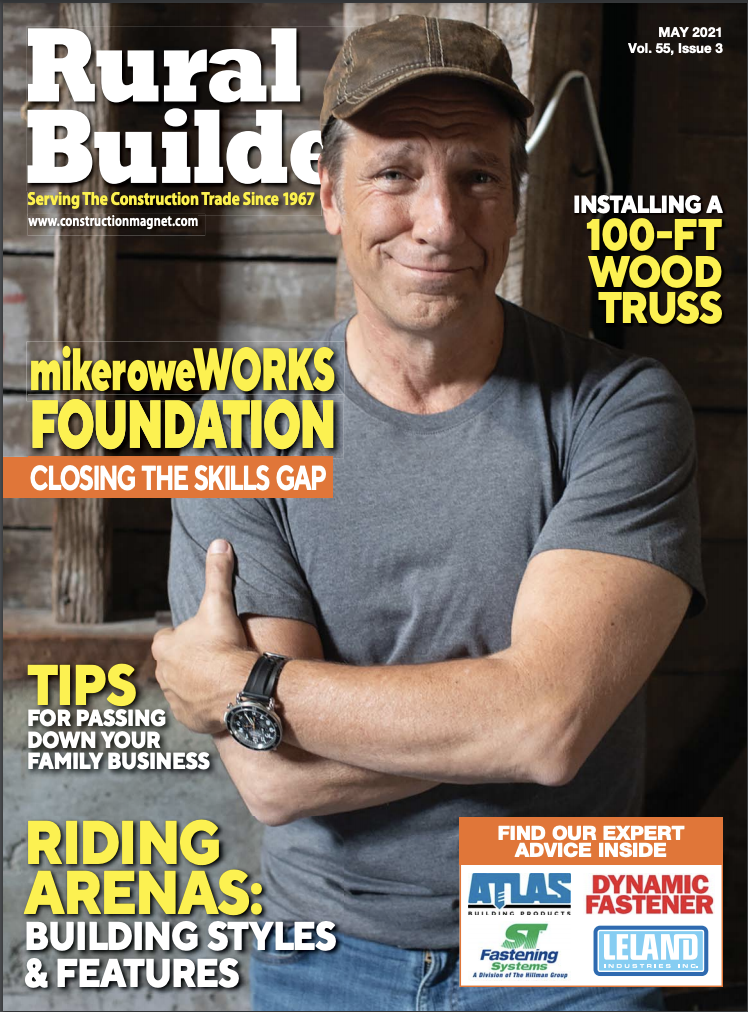