By Rocky Landsverk
The American landscape has always been highlighted by our biggest structures, and typically they’ve been from our farms. Big red barns, tall concrete silos, and silver cylindrical grain bins made our drives across the country just a little less boring, all the while helping us create affordable food.
Advancements and trends through the years have led to more, and bigger, grain bins. They have been in favor versus silos for decades and just keep getting larger; Sukup has now set the standard twice, building two record-sized bins for Golden Grain Energy. Their diameter is 165 feet (55 yards) and they hold 2.25 million bushels.
As a contractor or developer, you might need to help a client plan for a grain bin. We asked a group of experts on the matter — people who work for grain bin manufacturers — for their advice.
What Is a Grain Bin?
A silo is the taller, narrower structure that we all know. They are typically made of concrete and are almost always round. A grain bin is the huge, round metal structure you’ll see on modern farms. Silos traditionally hold silage, which is grass or other green and wet fodder, usually for dairy cattle. Grain bins store dry corn and soybeans, sometimes for domestic use but often for the export market.
About half of all grain is now stored “off farm,” sometimes meaning at a coop or shared structure, and sometimes simply meaning at a massive mega-farm’s storage property. “On farm” means it’s stored near the place where the animals and people live.
The Basics of a Grain Bin
There are a lot of decisions to be made when planning or purchasing a grain bin. There is a lot of machinery involved to move this grain around, both inside and outside the bin, and many companies sell the pieces and parts that will move the grain around. Meanwhile, other companies sell the bin itself, and this article will focus on the decisions involved with planning for the bin.
Keith Timmermeyer works for GMLS Industries from Peabody, Kansas, which makes Golden Grain bins. He said in general, in the southern United States people are looking for storage bins, while drying bins are often built in northern areas. Storage bins will have an aeration floor and a fan. A drying bin will have a heater and a recirculating device, like a “stir-ator.”
He will use criteria like this when deciding how to help a
customer plan for their bin:
• Is this for storage or drying or both?
• Are you feeding out of it? If so, you need an unload auger.
• What crops might go into this? That impacts things like the type of floor.
• Do you want or need modern electronics like Wi-Fi and apps?
• Are you a small farm (by today’s standards) or is this a commercial operation?
The type of crop impacts the floor and the equipment you’ll put into the bin. Some crops and situations might utilize a 6-inch auger, and others would use 8-inch or 10-inch. Corn, wheat, beans, and similar products would use one type of floor; other grains require a different floor. One expert told us millet “is like pepper and would fall right through” the typical floor.
Choosing the Right Bin

The basic decisions to be made when choosing the right grain bin include what it will be used for. Is it long-term storage or is it a wet tank? A wet tank is a working bin that is constantly being turned. “Wet grain can start a fire,” said Shad Singleton, North American Sales Manager for Chief Agri.
Beyond the bin-buying process, there are a lot of equipment options. “You can batch-dry, you can continuously load-dry. You might need an air permit, because you are emitting dust,” Singleton said. This article is meant to focus on the first decision — planning for and purchasing the bin.
Choosing the Right Size
Grain bins are enormous, of course. That’s kind of the point. But how big is too big?
“Larger is not always better but can be more cost-effective,” said Randy Coffee, VP of sales & marketing for Superior Grain Equipment. “As a bin gets larger in bushel holding capacity, the cost per bushel to purchase/erect goes down. Planning for expansion is always good practice. Peak heights and centers of bins should be considered as well as uniformity in bin sizing for simplification.”
Choosing the Location Part 1:
Ground/Foundation
Choosing the right location comes first, and that decision will be impacted by factors including electrical power availability, the ground’s ability to hold a structure this large, and traffic concerns related to not only the size of the bin, but also the trucks and tractors that will be in the area.
The need for a solid foundation is one of the first things that will impact the location of the bin. For large commercial projects, you might be drilling pilings. “Have you done any borings?” Singleton said. “A lot of projects get put on hold because the soil was bad (and couldn’t support a huge grain bin).”
For a lot of builders, that means contacting a company like Terracon and sending core samples of the soil. “Based on that core sample, you can get an engineer involved,” Singleton said. “You might need something like an over-excavation, or compacted fill, or it might require piling. You hope that a simple soil correction will solve the problem, vs. having to do piling.”
Choosing the Location Part 2: Traffic
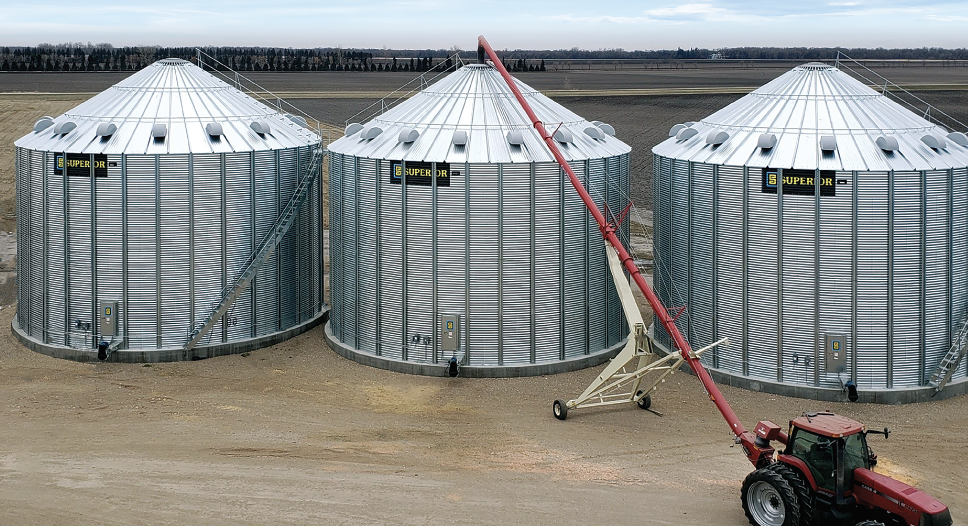
Most often, the farmer or company involved knows their usage and traffic situation and they simply need to be reminded to consider it. “What is your traffic flow through the farm and through the commercial elevator?” Singleton said. He said it’s more common than you might think to wind up needing to call the highway department. “You might even have to put a turn lane in off the highway,” he said.
Coffee said to also remember the intra-farm traffic. “You want a site that is easy to get in and out of to maximize efficiency and lessen accidents and bottlenecks,” Coffee said. “You also want the grain flow between receiving and loading out to take the easiest and shortest path.”
Choosing the Location Part 3: Power
Both Coffee and Singleton strongly suggested that your client figure out how to get three-phase power.
“If a site is limited on power, such as a single-phase application, considerations can be given to a generator setup or talking to the power company about bringing in additional service or possibly a new three-phase service,” Coffee said. “If a site is completely limited, sometimes that may not be the correct site choice.
“Fan sizing is determined by power available but also by proper airflow, which may push you into the dilemma of not having enough power. Some of these decisions are a back-and-forth between what is available and what is the proper way to do it and one selection may hold more weight over another.”
Your equipment is going to include unloaders, fans, exhausters, etc. “Do you have three-phase power? Some farms don’t have it, and then you’re limited in horsepower,” Singleton said.
So, like the fact that you might be getting the highway department involved because these are so huge that they might require a road to move, you might also wind up calling the power company.
“I’ve seen new substations put in,” Singleton said. “There are towns in North Dakota where the grain elevator requires more power than the entire rest of the town combined. We can tell you the horsepower required.”
Other Options to Consider
Refurbish or Buy New?
If your customer has purchased a large facility and the bin manufacturer is long gone, do you need to start from scratch, or can you add new rings to make it stronger again?
“Even if a bin has stood with no issues for, say, 40 years and is still sound, you may want to save some money by trying to make it larger,” Coffee said. “Or even when talking about a newer bin, the sheets are usually designed with a weight load based on structural engineering criteria that are not designed to handle just simply adding rings, especially on older bins where you cannot get exact replacement sheets because the manufacturer is out of business or whatever the case may be. Sometimes the cost factor may just need to be looked at as ‘this bin cost X amount per year for the last X amount of years and it was a great value, but it has reached its end of life.’ The cost of replacing new versus trying to retro the old is, long term, a better strategy.”
Do You Need Wi-Fi?
Timmermeyer is “old school” and serves more traditional farmers — you might call them farmers of the ’70s and ’80s. He readily admits that megafarms and commercial operations will want upgrades like continual-flow dryers, and Wi-Fi that runs apps that can turn on fans and remotely monitor moisture. But he believes those options are often unnecessary.
“If you go to western Kansas, with 8,000 acres, they’re not going to listen to me,” Timmermeyer said, only somewhat jokingly. “They want a continuous flow dryer, so they can keep fewer hands. There are even companies that promote Wi-Fi with apps, to turn off fans, and etc.”
Timmerman is not a big fan of Wi-Fi in part because lightning so often hits grain bins. “A grain bin is the tallest metal structure in an area,” he said. “Through my years, I couldn’t count how many I’ve known that have been hit by lightning.” RB