I’d first heard rumblings of a wood shortage earlier this spring, but it wasn’t until summer that I saw it first-hand. A trip to our local lumber yard revealed bare shelves that were normally overflowing with product—a mere handful of treated 2 x 4s remained in the many slots dedicated to this popular size.
After a quick internet search for “lumber shortage 2020,” most of the articles and news briefings you’ll find are about how this shortage is affecting the residential market (which has been booming). According to the National Association of Home Builders (NAHB), since mid-April of this year, the composite price of lumber “has soared more than 170%. This surge is adding approximately $16,000 to the price of a new single-family home and more than $6,000 to the average new apartment.” But of course there are many other areas of construction that rely on wood as a primary resource, especially the post-frame industry.
Small town newspapers are even reporting this issue on their front pages, including in the July 9 issue of a Mississippi community paper called the South Reporter. There, you’ll find the dramatic story of a Chicago-based contractor who was forced to travel more than 500 miles to procure a large purchase of treated lumber. And the supply isn’t looking much better today.

What Are the Causes?
Prior to the start of the COVID-19 pandemic, there were already tariffs on wood between Canada and the U.S. (a hefty 20% on treated lumber) that were causing issues. Introduce a global health crisis to the mix, and a shortage was inevitable. As states sought to slow the spread, they implemented statewide restrictions on what companies were deemed “essential,” in effect shutting down many industries including the wood treatment facilities. As plants were slowly allowed to reopen, new restrictions on operations, allowing for social distancing, have made it difficult for the supply to “catch up” with a surprisingly increasing demand.
This demand is happening because a huge portion of the U.S. population has been and is still working from home, which allows them time to get to their “someday” projects like decks, fences, sheds, and barns. This might sound like good news at first! Any money budgeted toward a vacation may be poured back into home projects instead, since they can’t go anywhere and might as well enjoy their surroundings.
In fact, many contractors (and manufacturers) we’ve recently talked with are having an incredibly busy and successful year, despite initial concerns when the pandemic first hit. But, with busy contractors comes the need for more materials, so now you don’t just have the DIY crowd scrambling for those last few 2 x 4s on the shelf—contractors have been forced to search out supplies at every local and even long distance lumber yard around.
Alternative Materials
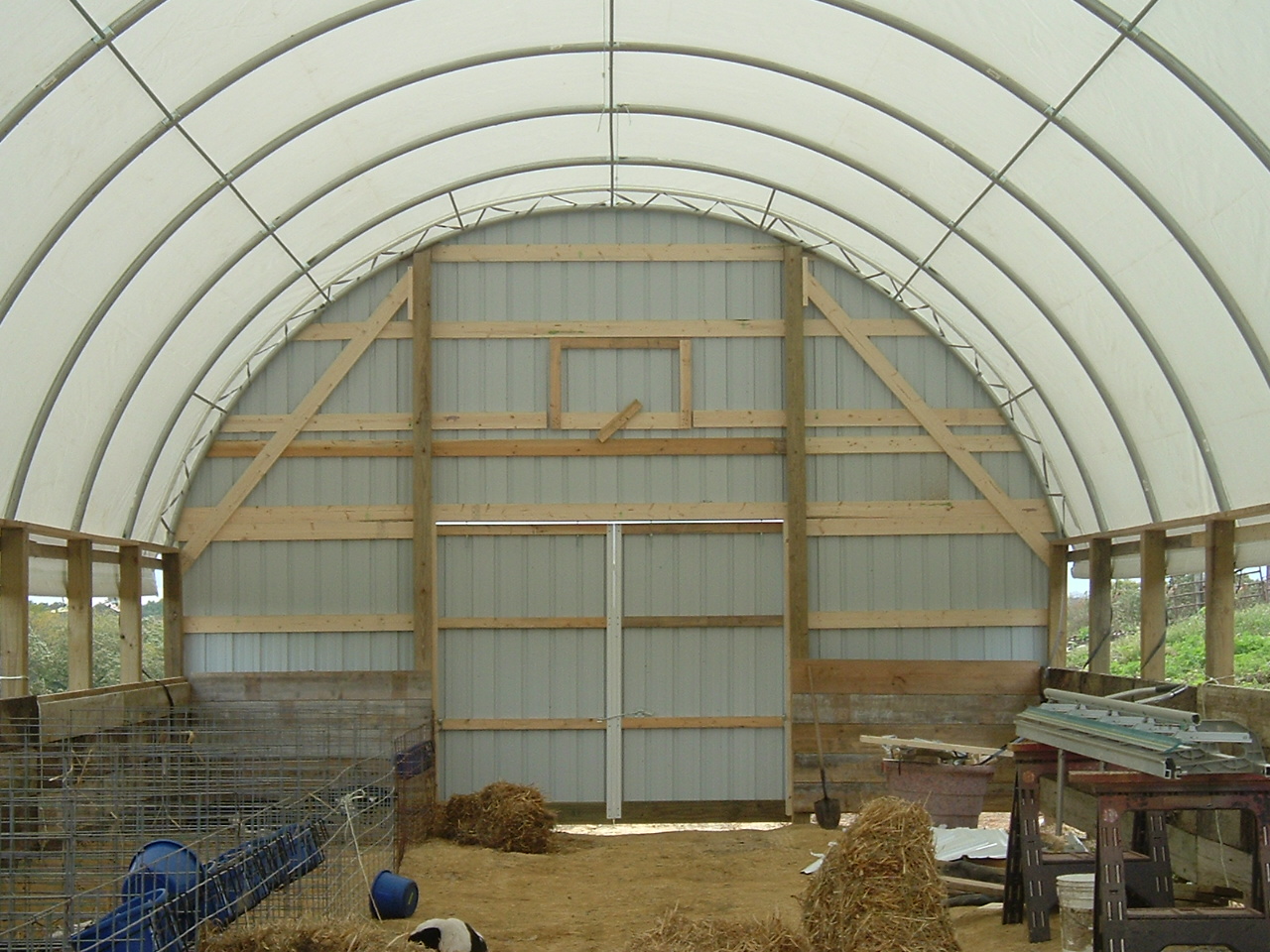
A recent poll conducted in one of our weekly e-newsletters revealed that 75% of contractors are interested in or are already pursuing alternative materials as this wood shortage continues.
One alternative is to explore the world of metal framing, even if only for the short term until this shortage is remedied. David Ruth, President of Freedom Mill Systems, has seen a dramatic increase in sales of cold-formed steel tubing machines. According to Ruth, contractors are tired of standing in line, waiting for every wood shipment, so they buy their own machines to produce their own materials. To get started with this method (other than the obvious amount of research needed), Ruth suggests the following must-have list:
• A large enough building to house the equipment and the products — they are producing 10’ to 20’-long products, and the tube mill itself can be 100’ to 150’ long
• A source for steel and the money to buy it
• Employees to train (Freedom does offer training)
Another option to look at is tension fabric buildings, especially for agricultural customers. Jon Gustad, Building Sales Manager for ProTec, shared how easy of a transition this is for post-frame builders: “When ‘wood guys’ think anything steel frame related, they tend to assume that welders and cutting torches will be involved. In reality, the existing skills and tools of most wood builders are more than sufficient for many of our tension fabric buildings. With proper planning, these buildings go together as easily as an Erector Set.” To make it even easier, they offer unlimited resources to those who make the switch.
Still other builders are researching the options available in the engineered lumber market. According to Craig Miles, Director, National Sales and Marketing OSB for LP Building Solutions, “We engineer value and multiple benefits into our products. And for builders, products that minimize corrections on the job and drive quality construction are huge advantages.” They offer one of the industry’s strongest, stiffest sub-floors, which also features more strands, resin, and wax to provide exceptional moisture resistance.
If you plan on sticking with wood and continuing the hunt for materials, the NAHB suggests adding an escalation clause to your contracts. This allows for you to charge the project owner for up to a predetermined percentage of material cost increase—something useful today.
A Positive Outlook

Many large manufacturers and even smaller kit suppliers are envisioning a return to “normal” soon. Miles shared, “Where we did see builder sentiment, home sales, and demand for LP’s products drop at the beginning of the pandemic, these have rebounded sharply and continued to climb, and we have returned to full production.” To give you the best chance of getting that lumber you need, when you need it, try these techniques: Buy it when you can, not when you need it; ask about preordering; ask about bulk orders, even if its more than you normally need; ask if paying ahead or paying with different terms will get you to the front of the wait list; and ask if the lumber yard has any sister stores or other supply options where the materials can be transferred between them with pre-sales.
As we hear more from industry experts, we’ll be sure to share every bit of information with our readers. RB